Process Control Facilities
ATC has in house chemical testing laboratory to control, monitor, and maintain the chemical and DI water used in the production floor. The laboratory is also equipped with a type of testing instrument capable of doing in house periodical testing base on the plating specification requirement.
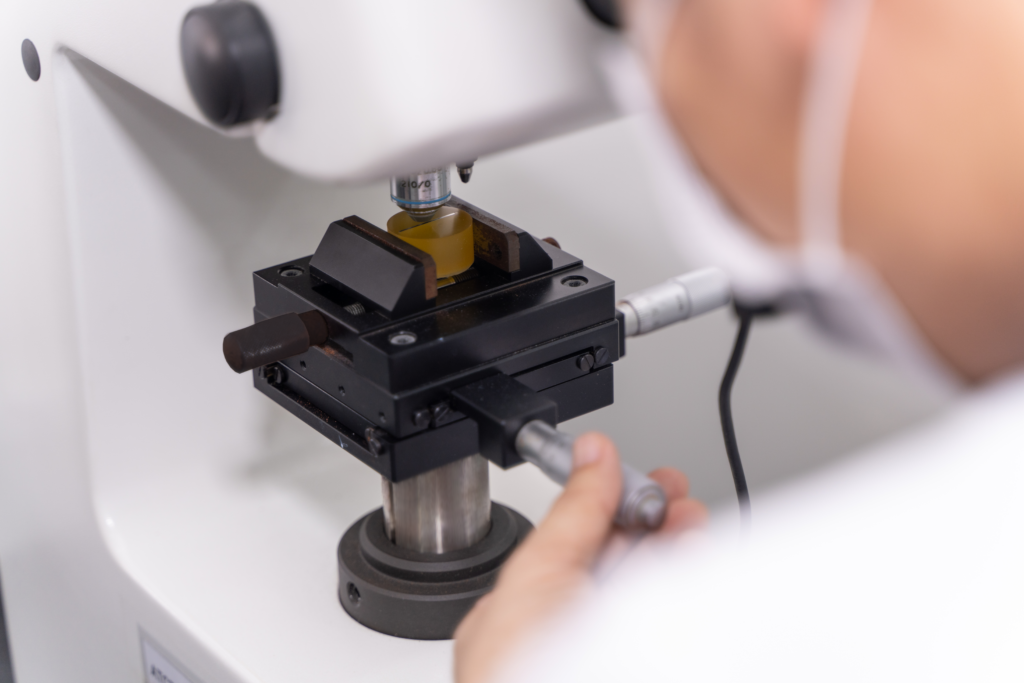
Laboratory
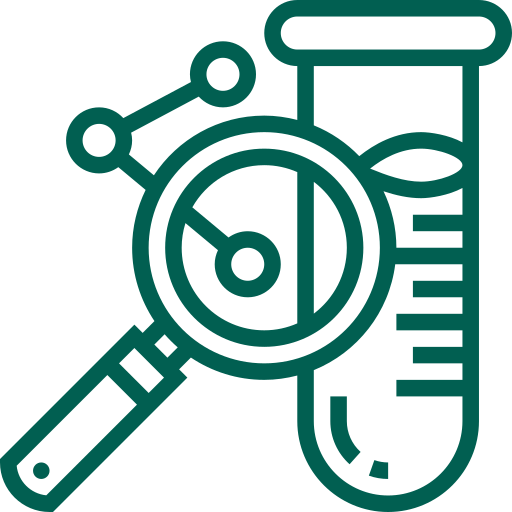
Chemical Bath Analysis
Chemical bath analysis is an essential step in process control, as it safeguards the consistency and quality of produced goods. Bath analysis makes use of analytical techniques such as titration and pH measurement to attain quick and precise measurements of all solutions used.
Regular chemical bath analysis is done to ensure parameters such as: conductivity of water rinse solutions and plating bath concentration are maintained within the specification limits throughout the production run. The frequency of bath analysis is customized to suit the sensitivity of each process.
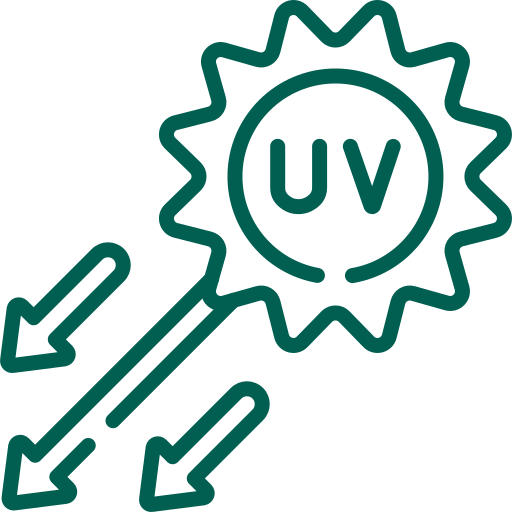
Ultraviolet (UV) Spectroscopy
Colouring of plated goods through the use of dyes has been a staple process at ATC. The UV Spectroscopy method has been employed to reliably assess the dye solutions and maintained consistently at the optimum level.
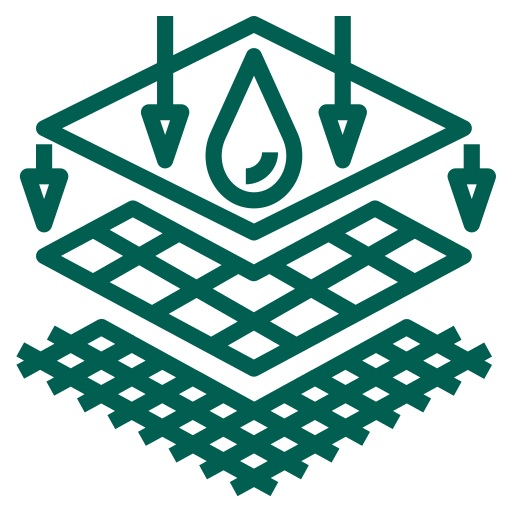
Flame atomic absorption spectroscopy (FAAS)
In taking a step further to achieve tighter controls over our bath solutions, ATC has employed the FAAS machine to greatly enhance our analytical arsenal. FAAS allow us to accurately quantify a wide array of metals down to the “ppm” level, granting us the ability to perform thorough analysis whenever required.